
And generally I think it’s losing steps here and there as it cuts, though they don’t always show up.ĭo you think it might be hitting the dustboot? Could that account for it? I don’t see any kind of plunge on that tool path that should cause it to lose z-steps, so I’m really not sure what else it could be. So, it seems the z-height wasn’t wrong, after all. I reset the Z-zero to the top of the stock, and ran the next job, which cut down into the wasteboard by 3.325mm. After the job was over I checked the z-height, and it seemed to be off by 3.325mm. 25” Adaptive Clearing" pass, I thought I heard it lose a step or two, but then I couldn’t see any issues, so I let it go on with its work. The other issue I ran into was a very mysterious Z-height problem. The other circles are all fine, so I’m going to run it all again and see what happens. On the largest circle, the little lip halfway down is supposed to 5mm wide, but it’s only 3mm. The first is that the dimensions of the finished parts are not correct.

For the most part they all worked perfectly! I ran the file - actually I broke it up into individual jobs so I could see what was working and what wasn’t. Ok, so first, once again, thank you very much! This level of help is truly incredible. hopefully you have a Suckit or other fixed-height dust shoe, to mill at 30mm depthĪLL of this being said, this is just me playing with your file, there might be some mistakes left in there, absolutely do verify everything if you want to use it !.I took a look at the feeds and speeds, and they looked OK so I did not change anything (3flute, 18000RPM, 100ipm => 0.018" chipload, should be ok in hardwood).I did not bother about finishing passes on the INNER walls, if this matters you should add them.I would instead use an upcut for the adaptive clearing, and then switch to a downcut for the finishing contour passes only I personnally wouldn’t use a downcut for adaptive clearing at such depths (30mm). downcut endmills are great to avoid tearout on top surfaces, BUT they also have poor chip evacuation.optimal load of 2.54mm may be a bit high (to my taste) even in wood: you can try it, and dial it down if you feel the machine struggling.Here are a few more things I would consider: Here’s my edited version of your file with the modifications listed above:
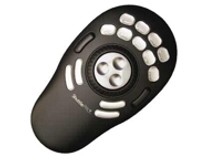
Contour shuttle fusion 360 skin#
I added -0.1mm axial stock to leave, to overcut slightly and make sure you don’t have an onion skin left at the bottom.I did the toolpaths assuming my workholding method (tape & glue), so you may need to tune that. note: I added the adaptive clearing on the small circle, it may not work well with your workholding method of screwing the piece in the center.Same principle as doing profile cuts last. This is to go from the inside to the outside of the stock, such that there is always a maximal amount of material left to hold the piece being cut.
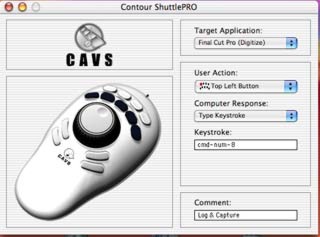
I rearranged the toolpaths in the opposite order: cutting the small circle first, then the medium, then the large.During the second pass, the shank will slightly rub against the wall cut during the 1st pass, but…sometimes it’s not a big deal and you can get away with it.
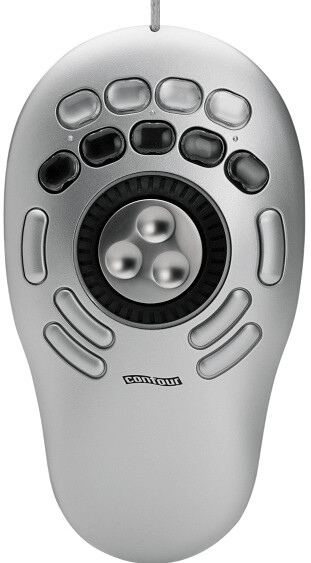
Say 15mm: during the first pass, everything will be allright. But, it’s not always easy to find an endmill with a long LOC like that, so you can choose to go ahead and use your endmill with its 3/4" LOC, and use a stepdown value that is lower than the LOC. This will remove the “collisions” that F360 reports.
